Accessment of latex stability
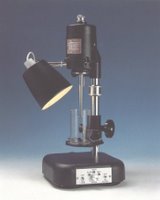
Manufacturer: How do you normally test for the stability of latex as regards its processability?
-----------------
JW Latex Consultants (Rubber Consultants 乳胶顾问) offer solutions to problems in Rubber Technology and Latex Technology (Natural Rubber latex and Synthetic Rubber latex) pertaining to processing and the manufacturing of latex products (condoms, catheters, medical gloves, baby teats/soothers, toy balloons etc) Quick answers through e-mails are possible at reasonable cost.
Contact John Woon at john@jwlatexconsultants.com and woonsungliang@yahoo.com.sg
JW Latex Consultants (and Rubber Consultants,乳胶顾问) offer solutions to your problems in Natural Rubber latex and Synthetic Rubber latex processing and the manufacturing of latex products (condoms, catheters, medical gloves, baby teats and soothers, toy balloons etc) Quick answers through e-mails are possible at reasonable cost.
![]() |
---|
可以通过电子邮件与JW乳胶顾问来解决问题
Please kindly donate to support the maintenance of this site. We'd appreciate it very much.
Manufacturer: We are making some rubber products using Neoprene (Polychloroprene) as the base polymer. Due to the high cost of this rubber, we're thinking of adding NR to reduce the recipe cost. What is the maximum level of NR we could at?
Manufacturer: We make household gloves with reasonable quality which give us quite good ROI for some years. But we believe this could improve if we could overcome the occasional problem of poor flocking of our gloves i.e. the flocks tend to disappear after washing. Any good ideas?
JohnWoon:This question had been raised before. But there is no harm in repeating my comment and recommendation. The basic objective is to have good penetration, anchoring and bonding of the individual strands of the flock onto the latex layer. However over penetration would result in the unwanted total submersion of the flocks. Hence you have to strike a balance between the two extremes.
Please try the following suggestions:
1) Ensure the coagulant for the first latex dip is not too strong otherwise the unused residual coagulant would migrate to the subsequent second latex layer (sometimes referred to as the adhesive layer) leading to premature gelling of this second latex layer. This latex must remain fluid at the time of flocking while in the flocking chamber.
3) Increase the latex viscosity by adding a suitable thickener at the right level. This would increase the thickness of the adhesive layer.
Manufacturer:We are producing rubber products based on Natural Rubber. Some of these products must be "submerged" in the soil for many years. Since NR is well known to be biodegradable, we need to prevent this as far as practically possible. For reason we cannot reveal, switching to synthetic polymer is not acceptable. Your assistance would be appreciated.
I suggest you try the following ideas:
2) As normal organic waxes would trigger and increase biodradability, this material must be avoided or replaced with chlorinated wax.
Latex Producer: What damage can bacteria do to NR latex and how to prevent this?
Manufacturer: We are adhesive manufacturer and started to buy NR latex in 200 kg steel drums about a year ago. Whenever we want to use the latex, we always find a thick layer of latex at the top of the drums. This has given us some problems. How can we prevent this?
Do not discard the "thickened" or "creamed" latex unless it has dried to solid state. This latex is still reversible when remix in normal latex.
Manufacturer: You seem to be an advocate of Prevulanised latex. Why?
Manufacturer:I understand you have answered this question of mine some time back. But hope you could answer again. My question: Is vulcanization of Natural Rubber latex similar to that of the dry rubber? What is the mechanism involved?
John JohnWoon: The possibility of vulcanizing the rubber molecules within the dispersed rubber particles in the Natural Rubber (NR) latex was first investigated by Philip Schidrowitz in the period 1914 – 1918. His idea was to use prevulcanised NR latex for making latex foam products in order to eliminate the vulcanization stage for economical reason.
(However, with some modification, a "hybrid" system based on prevulcanised latex could now be used successfully for making foam products such as mattresses and pillows).
Prevulcanised latex is therefore a compounded latex in which the molecules of the rubber particles are chemically cross-linked (i.e. vulcanised). However there is no change in rubber particle size, shape and particle size distribution, the latex still retaining its original fluidity and colloidal property.